Glass insulator
Material Selection: GTMS typically involves a glass component and a metal component. The choice of materials depends on the specific application and the desired properties of the seal.
Common metals used include stainless steel, Kovar, and nickel-based alloys, while various types of glass compositions are selected based on their thermal expansion coefficients and chemical resistance.
Design and Preparation: Engineers design the shape and dimensions of the metal and glass parts to be sealed. The metal component is often machined or fabricated to the desired shape, while the glass component may be formed through processes like extrusion or molding.
Cleanliness: One critical aspect of GTMS is ensuring that both the metal and glass components are meticulously cleaned and free from contaminants, such as oils, dirt, or oxides, which can interfere with the sealing process.
Assembly: The glass and metal components are carefully aligned and brought into contact with each other in a controlled environment. The assembly is often done in a vacuum or controlled atmosphere to prevent the introduction of impurities.
Heat Sealing: The assembly is subjected to controlled heating to melt the glass. The glass flows and adheres to the metal surface, creating a hermetic seal as it cools and solidifies. The thermal expansion properties of the materials are critical to ensuring a strong, stress-free seal.
Cooling and Annealing: After sealing, the assembly is slowly cooled to room temperature to relieve internal stresses and improve the seal’s integrity. This process, known as annealing, helps reduce the risk of cracks or leaks in the seal.
Quality Control: The finished glass-to-metal seal is subjected to rigorous quality control tests to ensure its hermeticity and reliability. This may include leak testing, electrical testing, and visual inspection.
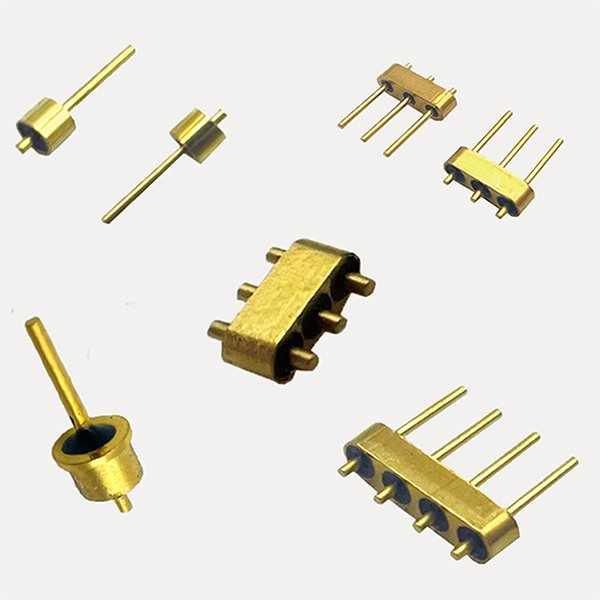