1.What should we do to design EMC products?
Answer: To meet the functional requirements of the product, reduce the debugging time, and make the product meet the requirements of the electromagnetic compatibility standard, so that the product will not produce electromagnetic interference to other equipment in the system.
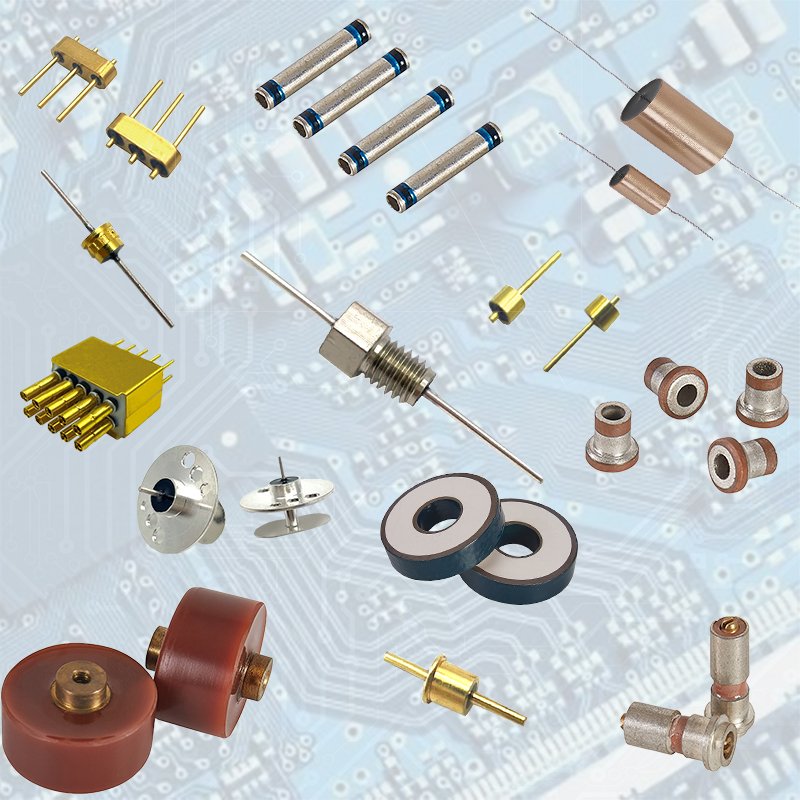
2. From which aspects can the electromagnetic compatibility design of the product be carried out?
Answer: Circuit design (including device selection), software design, circuit board design, shielding structure, signal line/power line filtering, circuit grounding design.
3. In the field of electromagnetic compatibility, why is it always described in decibels (dB)?
Answer: Because the amplitude and frequency range to be described are very wide, it is easier to express it in logarithmic coordinates on the graph, and dB is the unit when expressed in logarithm.
4. I don’t know much about EMC, but now the data transmission rate in circuit design is getting faster and faster. When I made the PCB, I also encountered some EMC problems of PCB, but I felt too latent. I want to study well in this area, not just follow the trend, I will learn what everyone learns. I really think that EMC will become more and more important in the future circuit design, as I said earlier, I don’t know much about it, and I don’t know how to get started. I want to ask what basic knowledge is needed and what basic courses should be learned to do a good job in EMC. How to study is a better way. I know that it is not easy for any subject to learn well, and I have never thought about getting him in a short period of time. I just want to give some advice and try to avoid as many detours as possible.
Answer: About EMC, you need to first understand the EMC standards, such as EN55022 (GB9254), EN55024, and simple test principles. In addition, you need to understand the use of EMI components, such as capacitors, magnetic beads, differential mode inductors, common mode inductors, etc., At the PCB level, you need to understand the layout of the PCB, the stacking structure, the impact of high-speed wiring on EMC, and some rules. Another point is that you need to master some analysis and solution ideas for EMC problems. These are the basic knowledge that must be mastered as a hardware person in the future!
5. A newbie who has just set foot in PCB design, I would like to ask, what kind of knowledge should I master in order to do PCB design? In addition, where can I find the knowledge about safety regulations encountered in PCB design? Your advice is greatly appreciated!
Answer: For PCB design, you should master:
1. Familiar with and master related PCB design software, such as POWERPCB/CANDENCE, etc.;
2. Understand the specific architecture of the product you are familiar with, and be familiar with the schematic circuit knowledge, including digital and analog knowledge;
3. Master PCB processing flow, process, and maintainable processing requirements;
4. Master the knowledge of PCB board high-speed signal integrity, electromagnetic compatibility (emi and ems), SI, PI simulation design, etc.;
5. If the related work involves radio frequency, you need to master radio frequency knowledge;
6. For the regulatory knowledge of the PCB design site, mainly see GB4943 or UL60950, the general insulation spacing requirements can be obtained by looking up the table!
6. Basic principles of electromagnetic compatibility design
Answer: Electronic circuit design guidelines Electronic circuit designers often only consider the function of the product without comprehensively considering the function and electromagnetic compatibility. Therefore, while the product completes its function, it also generates a lot of functional harassment and other harassment. Moreover, the sensitivity requirements cannot be met. The electromagnetic compatibility design of electronic circuits should be considered from the following aspects:
Component selection In most cases, the degree to which the basic components of the circuit satisfy the electromagnetic characteristics will determine the degree to which the functional unit and the final device satisfy the electromagnetic compatibility. The main criteria for selecting suitable electromagnetic components include out-of-band characteristics and circuit assembly technology. Because whether electromagnetic compatibility can be achieved is often determined by the response characteristics of components away from the fundamental frequency. In many cases, circuit assembly determines the out-of-band response (such as lead length) and the degree of coupling between different circuit components. The specific rules are:
(1) At high frequencies, compared with lead-type capacitors, priority should be given to using feedthrough capacitors or support capacitors with small lead inductance for filtering.
⑵When lead-type capacitors must be used, the influence of lead inductance on filter efficiency should be considered.
(3) Aluminum electrolytic capacitors may have a temporary dielectric breakdown of a few microseconds. Therefore, solid capacitors should be used in circuits with large ripples or transient voltages.
⑷Use resistors with small parasitic inductance and small capacitance. Chip resistors can be used in ultra-high frequency bands.
⑸ Large parasitic capacitance of large inductance, in order to improve the insertion loss of the low frequency part, do not use a single section filter, but should use a multi-section filter composed of several small inductors.
⑹Saturation characteristics should be paid attention to when using the magnetic core inductance, especially the high level pulse will reduce the inductance of the magnetic core inductance and the insertion loss in the filter circuit.
⑺ Try to use shielded relays and ground the shielded case.
⑻ Use input transformers with effective shielding and isolation.
⑼ The power transformer used for sensitive circuits should have electrostatic shielding, and the shielding shell and the transformer shell should be grounded.
⑽The interconnection signal lines inside the equipment must use shielded wires to prevent harassment coupling between them.
⑾In order to connect each shield to its own pin, a plug socket with enough pins should be selected.
7. The problem of square wave pulse driving inductive sensor
answer:
1. During the signal test, try to do it in a shielded environment. If it is inconvenient, at least shield the sensor and the front stage.
2. Use a differential probe as much as possible during the test, or at least reduce the length of the ground wire of the probe as much as possible. This can reduce test errors.
3. The actual working frequency of your circuit is not too high, you can reduce the ringing by wiring. For better noise characteristics, consideration should be given to the suppression of common-mode signals. If necessary, a conjugate reactor should be inserted. At the same time, pay attention to the switching power supply noise in the entire working environment and avoid power supply coupling.
4. If the sensor allows, you can use the current amplification mode, which is beneficial to increase the speed and reduce noise. The analog switch is placed after the preamplifier as much as possible. Although there is one more preamplifier, the performance is improved a lot and the debugging difficulty is reduced.
5. If you really care about the waveform, consider additional frequency compensation. If it is only digital detection, the operating frequency should be reduced. In a word, low frequency can be low frequency, and straight can be straight.
6. Pay attention to anti-aliasing filtering before AD conversion and software filtering to improve data stability.
8. The phenomenon of GPS electromagnetic interference phenomenon: Especially GPS is applied to PMP products, the function is MP4, MP3, FM frequency modulation + GPS navigation function, handheld dual-use GPS terminal products, there must be a built-in GPS Antenna, such GPS The MCU, SDROM, crystal oscillator and other components on Antenna and GPS terminal products are prone to EMI/EMC electromagnetic interference, resulting in the GPS Antenna’s ability to receive satellites greatly reduced, and there is almost no way to locate normally. What measures can be taken to solve such EMI/EMC electromagnetic interference?
Answer: ESD Filter can be added on it, which has both anti-static and anti-electromagnetic interference. This method is used by our mobile phone customers with GPS function. There are many manufacturers that do this, such as Tektronix (Raychem), Jiabang, South Korea ICT and so on.
9. Almost all important signal lines on the board are designed as differential pairs. The purpose is to enhance the anti-interference ability of the signal. There have been many confusions:
1. Is the differential signal defined only in the simulation signal or digital signal or is it fixed?
2. In the actual circuit diagram, how to analyze the frequency response of the differential line pair as a filter? Is it the same as the method of analyzing the general two-port network?
3. How do the differential signals carried on the differential wire pairs be converted into general signals? What are the signal waveforms on the differential wire pairs and how are they related to each other?
answer:
1. The differential signal uses only two signal lines to transmit a signal, and a circuit that makes decisions based on the voltage difference between the signals can be either an analog signal or a digital signal. The actual signals are all analog signals, and digital signals are just the sampling results of analog signals quantized with threshold levels. Therefore, differential signals can be defined for both digital and analog signals.
2. The frequency response of the differential signal is good. The actual differential port is a four-port network, which has two analysis modes, differential mode and common mode. As shown below. When the analysis frequency is corresponding, a common-mode sweep source with the same polarity and a differential-mode sweep source with opposite polarities must be added separately. The corresponding terminal needs to set the common mode voltage test point Vcm=(V1+V2)/2, and the differential mode voltage test point Vdm=V1-V2 accordingly. There are many articles on the calculation and principle of differential signal impedance on the network, you can learn more about it.
3. The differential signal usually enters the differential driving circuit, and the differential signal is obtained after amplification. The simplest is the differential cascode mirror amplifier circuit, which is introduced in general analog circuit textbooks. The following figure is the spice circuit diagram and output signal waveform of a differential amplifier device, which generally requires them to be completely inverted, and have a sufficient voltage difference greater than the differential mode voltage threshold. Of course, the signal inevitably has a common mode component, so a very important indicator of the differential amplifier is the common mode rejection ratio Kcmr=Adm/Acm.
10. I designed a speed control circuit for the DC magnet motor of the unit. The power end is not ideal after using 0.33uf + Sharp TV inductance + 0.33uf. Afterwards, 4 inductors are connected to the power end of the PCB board, but at 30 ~ What should I do if it exceeds 12db between 50MHz?
Answer: Generally speaking, LC or PI filter circuit is better than single capacitor filter or inductor filter. What do you mean when you use 0.33uf + Sharp TV inductance + 0.33uf for the so-called power supply terminal? Is it excessive radiation? In what frequency band? I guess in the DC magnet motor power supply loop, the feedback noise amplitude is large, the frequency is low, and the inductance filter with a larger inductance value is required. At the same time, the multi-stage capacitor filter is used, and the effect will be better.
11. Recently, I am trying to build a broadband amplifier with a range of 0-150M and a gain of not less than 80 DB. What questions should I pay attention to in terms of EMC?
Answer 1: Special attention should be paid to low noise when designing broadband amplifiers, for example, the power supply must be stable enough.
Answer 2:
1. Pay attention to the impedance matching problem of input and count, such as common base input and follow output
2. Uncoupling problems at all levels, including high frequency and low frequency ripple
3. Deep negative feedback, and prevention of self-oscillation and loop-back self-excitation, etc.
4. Design issues of bandpass filter gas
Answer 3: It’s really difficult to answer, you can’t see the actual design. All suggestions are still old-fashioned: pay attention to the three elements of EMC, pay attention to the conduction and radiation paths, pay attention to power distribution and ground bounce noise. 150MHz is the bandwidth of the analog signal. How fast is the rising edge of the digital signal? If the corner frequency is also below 150MHz, I personally think that conduction coupling and power plane radiation will be the main considerations. First, do the power distribution, division and decoupling circuit. 80dB, if the gain is high enough, do the isolation protection of the front minimum signal and its reference power supply and ground, and try to reduce the power supply impedance of this part.
12. Ask for EMC methods and issues in the design of small power DC permanent magnet motors. Produced a 90W DC permanent magnet motor (110~120V, speed 2000/min) EMC has been exceeding the standard. After production, the 16 slot was changed to 24 slot, and the shaft insulation was made, which failed to meet the standard! Now we have to design and produce 125W Motor, how to deal with it?
Answer: The EMC problem in the design of DC permanent magnet motors is mainly due to the back electromotive force generated during the rotation of the motor and the spark caused by the commutation. Specific analysis, you can use RMxpert to design and optimize the motor parameters, Maxwell2D to simulate the actual EMI radiation.
13. Can it be set by Impedance? Or use a similar layered impedance RLC resistance? Or use the designer to design the circuit and hfss to work together?
Answer: Concentrated resistance can be realized by RLC boundary; if it is thin-film resistance, it can be realized by surface impedance or impedance editing.
14. I’m doing an electrostatic test on a machine with a ring of metal decorative parts in the shell. I encountered: during the test, the 32k crystal oscillator is no problem when contact discharge is 4k, and the problem of stopping vibration when air discharge is 8k. How to deal with it?
Answer: If there is metal, the effect of air discharge is similar to that of contact discharge. It is recommended that you try to spray insulating paint on the metal bracket.
15. We are very troublesome to measure the electromagnetic radiation of PCB now. The spectrometer and the self-produced near-field probe are used. Not to mention the accuracy problem. The point of encountering a large voltage is very headache, fearing the damage of the spectrometer. I wonder if it can be solved by simulation.
Answer: First, EMI testing includes near-field probe and far-field radiation testing. No simulation tool can replace the actual test; second, Ansoft’s PCB single board noise and radiation simulation tool SIwave and high-frequency structure of any three-dimensional structure The emulator HFSS can simulate the near-field and far-field radiation of single boards and systems, as well as EMI radiation in a limited shielded environment. The effectiveness of simulation depends on your consideration of the EMI problem you design and the corresponding software settings. For example, the differential mode or common mode radiation on the board, the current source or the voltage source radiation, etc. Based on some of our practice and experience, most of the EMI problems can be solved through simulation analysis, and compared with the actual test, the effect is very good.
16. I heard that Ansoft’s EMC tools generally simulate frequencies above 1GHz. The clock line with the highest frequency on our board is only 133MHz from the main chip to SDRAM. Most of the remaining frequencies are at KHz level. We mainly use the SI/PI design made by Hyperlynx, the operation is relatively simple, but the EMC of the whole board is still beyond the standard, affecting the picture quality. In addition, do your tools have an interface with Mentor PADS?
A: Ansoft’s tools can simulate signals from DC to frequencies above tens of GHz, but compared to other tools, the lossy transmission line model above 1GHz is more accurate. As far as I know, HyperLynx is mainly for the simulation of SI and crosstalk, as well as the EMI radiation analysis of a single signal line. At present, there is no PI analysis function. There are many reasons that affect the EMC of the board. Solving signal integrity and crosstalk is only one aspect of EMC. Power plane noise, decoupling strategies, shielding methods, and current distribution paths all affect EMC indicators. These can be investigated by simulation in the SIwave tool of Ansoft. Supplementary note, ansoft’s tools have an interface with Mentor PADS.
17. Please explain when to divide the bottom layer to reduce interference, and when to use the ground partition to reduce interference.
A: I haven’t heard of splitting the bottom layer. What do you mean? Can you give an example? The stratigraphic division is mainly to improve the isolation between the disturbing source and the interfered body, such as the isolation between digital and analog. Of course, segmentation will also bring about signal integrity problems such as cross-segmentation. Using Ansoft’s SIwave can easily check the isolation between any points. Of course, there are other ways to improve the isolation, layering, decoupling, single-point connection, are all ways, the effect of specific applications can be simulated by software.
18. Capacitors are connected across two different power supply copper foil partitions as a return path for high-frequency signals. It is well known that capacitors are blocked from DC to AC, The higher the frequency, the smoother the current. My doubt is that most of the levels connected to PCBs today are After considering AC, what does the capacitor pass as mentioned above? “AC signal”?
Answer 1: This question is a bit mysterious. I have never seen a very convincing explanation. For AC, the ideal is that the power and ground are “short-circuited”, but in fact the impedance between them cannot really be zero. The capacitance you mentioned cannot have too much capacity to reflect the principle of “grounding at low frequencies and grounding at multiple frequencies”. This is probably the value of the capacitor. It is often encountered that after the connection of two components each with a power supply, some inexplicable interference is generated. A ceramic capacitor is used between the two power supplies to eliminate the interference.
Answer 2: The capacitor is used for voltage stabilization and EMI, and the AC signal is used. “Most of the current levels connected to the PCB are considered after AC”. This is true, but don’t forget that the digital circuit itself will generate AC signals and cause interference to the power supply. When a large number of switch tubes act at the same time, the power supply The resulting fluctuations are very large. However, in practice, this kind of capacitor is mainly used as an auxiliary function to improve the performance of the system. If it is well designed elsewhere, it can be completely eliminated.
Answer 3: Communication is changing. For the so-called DC level, such as a power supply, due to the impedance of the wiring, when its load changes, the demand for the power supply will change, large or small. In this case, the “series” wiring impedance will produce a large or small voltage drop. As a result, there is an AC signal on the DC power supply. The frequency of this signal is related to the frequency responsible for the change. The role of the capacitor is to store a certain amount of charge energy nearby, so that the energy required for this change can be obtained directly from the capacitor. Approximately, there seems to be an AC loop between the capacitor (which can be regarded as a power supply) and the load. Capacitors function as an AC loop, roughly like this…
19. The company has made a new mobile phone. During the 3C certification, one of the radiation indicators was not exceeded. The frequency is 50-60M, which exceeds 5dB. It should be caused by the charger. A few capacitors were added. Others did not. Capacitors have 1uF, 100uF. Is there any good solution (not changing the charger, only changing the mobile phone circuit). Can adding a capacitor to the input of the charger of the mobile phone board solve the problem?
Answer 1: The larger the capacitance is, the smaller the smaller one is, and the BIT is connected, but it is not very likely to be caused by the battery.
Answer 2: You try to short-circuit and shield the shell of the inverter inductor.
20. How can PCB design avoid high-frequency interference?
Answer: The basic idea to avoid high-frequency interference is to minimize the interference of high-frequency signal electromagnetic fields, which is called crosstalk. You can increase the distance between the high-speed signal and the analog signal, or add ground guard/shunt traces next to the analog signal. Also pay attention to the noise interference of the digital ground to the analog ground.
21. How to resolve the conflict between high-speed wiring and EMI in PCB design?
Answer: The resistance capacitance or ferrite bead added by EMI can not cause some electrical characteristics of the signal to not meet the specifications. Therefore, it is best to use the arrangement of traces and PCB stacking techniques to solve or reduce EMI problems, such as high-speed signals to the inner layer. Finally, the resistance capacitor or ferrite bead is used to reduce the damage to the signal.
22. Several PCBs form a system. How should the ground wires be connected between the boards?
Answer: When the signal or power supply between each PCB board is connected, for example, the A board has power or signal sent to the B board, there must be an equal amount of current flowing from the ground layer to the A board (this is Kirchoff current law) . The current in this formation will go back to the place with the lowest impedance. Therefore, at each interface where power or signals are connected to each other, the number of pins allocated to the ground layer should not be too small to reduce the impedance, which can reduce the noise on the ground layer. In addition, you can also analyze the entire current loop, especially the part with large current, adjust the connection of the ground layer or the ground wire to control the current flow (for example, create a low impedance somewhere, let most of the current flow from this Go somewhere) to reduce the impact on other more sensitive signals.
23. Can the ground wire be added between the differential signal lines in the PCB design?
Answer: Generally, the ground wire cannot be added in the middle of the differential signal. Because the most important point of the application principle of differential signals is to take advantage of the mutual coupling between differential signals, such as flux cancellation and noise immunity. If you add a ground wire in the middle, it will destroy the coupling effect.
24. What is the principle of properly selecting the point where the PCB and the shell are grounded?
Answer: The principle of selecting the ground point of PCB and housing is to use chassis ground to provide a low-impedance path to the returning current and to control the path of this return current. For example, in the vicinity of high-frequency devices or clock generators, you can use fixed screws to connect the PCB ground layer to the chassis ground to minimize the entire current loop area, which reduces electromagnetic radiation.
25. In the case of a fixed circuit board size, if the design needs to accommodate more functions, it is often necessary to increase the PCB trace density, but this may lead to enhanced mutual interference of the traces, while the traces are too thin also make the impedance Can not be reduced, please introduce the skills in high-speed (>100MHz) high-density PCB design?
Answer: When designing high-speed, high-density PCBs, crosstalk interference does require special attention because it has a great impact on timing and signal integrity. Here are some points to note:
1. Control the continuity and matching of trace impedance.
2. The size of the line spacing. Generally, the distance often seen is twice the line width. Through simulation, we can know the influence of trace spacing on timing and signal integrity, and find the minimum tolerable spacing. The results of different chip signals may be different.
3. Select the appropriate termination method.
4. Avoid the same direction of the traces of the two adjacent layers on the top and bottom, or even overlap the traces, because the crosstalk is greater than the case of adjacent traces on the same layer.
5. Use blind/buried via to increase trace area. But the production cost of PCB board will increase. In actual implementation, it is really difficult to achieve full parallel and equal length, but we still have to do our best.
In addition, differential termination and common mode termination can be reserved to mitigate the impact on timing and signal integrity.
26. In the PCB design, the filter at the analog power supply is often an LC circuit. But why is LC filtering sometimes worse than RC filtering?
Answer: The comparison of LC and RC filtering effects must consider whether the frequency band to be filtered and the choice of inductance value are appropriate. Because the inductance (reactance) of the inductor is related to the inductance value and frequency. If the noise frequency of the power supply is low and the inductance value is not large enough, the filtering effect may not be as good as RC. However, the cost to use RC filtering is that the resistor itself will consume energy, the efficiency is poor, and pay attention to the power that the selected resistor can withstand.
27. What is the method of selecting inductance and capacitance when filtering in PCB design?
Answer: In addition to considering the noise frequency that you want to filter out, the selection of the inductance value must also consider the reaction ability of the instantaneous current. If there is a chance that the output of the LC needs to output a large current instantaneously, too large an inductance value will hinder the speed of this large current flowing through the inductor and increase ripple noise. The capacitance value is related to the tolerable ripple noise specification value. The smaller the ripple noise value requirement, the larger the capacitance value. The ESR/ESL of the capacitor will also have an effect. In addition, if the LC is placed on the output of a switching regulation power, pay attention to the influence of the pole/zero generated by this LC on the stability of the negative feedback control loop. .
28. The problem of EMI and the problem of signal integrity are interrelated. How to balance the two in the process of defining standards?
A: The signal integrity and EMC are still in the draft and are not easy to disclose. How to balance the signal integrity and EMI is not a test specification. If you want to achieve a balance between the two, it is best to reduce the communication speed, but everyone do not approve.
29. How to meet EMC requirements in PCB design as much as possible without causing too much cost pressure?
Answer: The increased cost due to EMC on the PCB board is usually due to the increase in the number of ground layers to enhance the shielding effect and the addition of ferrite bead, choke and other high-frequency harmonic suppression devices. In addition, it is usually necessary to match the shielding structure of other institutions to make the entire system pass the EMC requirements. The following provides only a few tips on the design of the PCB board to reduce the electromagnetic radiation effect generated by the circuit.
1. Use devices with slower signal slew rate (slew rate) as much as possible to reduce the high frequency components generated by the signal.
2. Pay attention to the placement of high-frequency devices, and do not place them too close to the external connectors.
3. Pay attention to the impedance matching of the high-speed signal, the trace layer and its return current path (return current path) to reduce the reflection and radiation of high frequency.
4. Place enough decoupling capacitors on the power pins of each device to mitigate noise on the power and ground layers. Pay special attention to whether the frequency response and temperature characteristics of the capacitor meet the design requirements.
5. The ground near the external connector can be properly divided from the ground, and connect the ground of the connector to the chassis ground.
6. Ground guard/shunt traces can be used appropriately beside some particularly high speed signals. But pay attention to the influence of guard/shunt traces on the characteristic impedance of the trace.
7. The power layer shrinks by 20H than the ground layer, H is the distance between the power layer and the ground layer.
30. In PCB design, when there are multiple digital/analog function blocks in a PCB board, the conventional practice is to separate the digital/analog ground. What is the reason?
Answer: The reason for separating the digital/analog ground is because the digital circuit will generate noise in the power supply and ground when the high and low potentials are switched. The size of the noise is related to the speed of the signal and the size of the current. If the ground plane is not divided and the noise generated by the digital area circuit is large and the analog area circuits are very close, even if the digital and analog signals do not cross, the analog signal will still be disturbed by ground noise. That is to say, the method of non-dividing digital to analog can only be used when the area of the analog circuit is far away from the area of the digital circuit that generates large noise.
31. When designing high-speed PCBs, from what aspects should designers consider the rules of EMC and EMI?
Answer: General EMI/EMC design needs to consider both radiated and conducted. The former belongs to the higher frequency part (>30MHz) and the latter belongs to the lower frequency part (<30MHz). So you can’t just pay attention to the high frequency and ignore the low frequency part. A good EMI/EMC design must consider the position of the device at the beginning of the layout, the arrangement of the PCB stackup, the important online route, the choice of the device, etc., if There is no better arrangement for these in advance, and the solution will be more efficient with half the effort, and increase the cost. For example, the position of the clock generator should not be close to the external connector, the high-speed signal should go to the inner layer and pay attention to the continuity of the characteristic impedance matching and the reference layer to reduce Reflection, the slew rate of the signal pushed by the device is as small as possible to reduce high frequency components. When decoupling/bypass capacitors are selected, pay attention to whether their frequency response meets the requirements to reduce power layer noise. In addition, pay attention to high frequency signals The return path of the current makes the loop area as small as possible (that is, the loop impedance is as small as possible) to reduce radiation. You can also divide the ground layer to control the range of high-frequency noise. Finally, properly select the ground point of the PCB and the case (chassis ground).
32. In PCB design, how to reduce the EMI problem by arranging layers?
Answer: First of all, EMI should be considered from the system, PCB alone cannot solve the problem. For EMI stacking, I think it is mainly to provide the shortest signal return path, reduce the coupling area, and suppress differential mode interference. In addition, the ground layer is tightly coupled with the power layer, which is more epitaxial than the power layer, which is good for suppressing common mode interference.
33. Why do you lay copper when designing PCBs?
A: There are several reasons for copper laying:
1. EMC. For large areas of ground or copper power supply, it will play a shielding role, and some special grounds, such as PGND, play a protective role.
2. PCB process requirements. Generally, in order to ensure the electroplating effect, or the laminate is not deformed, copper is laid on the PCB layer with less wiring.
3. Signal integrity requirements, give high-frequency digital signals a complete return path, and reduce the wiring of the DC network.
Of course, there are reasons for heat dissipation, copper installation for special devices and other reasons.
34. Safety regulations: What are the specific meanings of FCC and EMC?
Answer: FCC: federal communication commission; EMC: electro megnetic compatibility. FCC is a standards organization, and EMC is a standard. There are corresponding reasons, standards and test methods for the promulgation of standards.
35. When making PCB board, in order to reduce the interference, should the ground wire form a closed form?
Answer: When making a PCB, generally speaking, the loop area should be reduced to reduce interference. When laying the ground wire, it should not be laid in a closed form, but rather in a tree shape. May increase the area of the ground.
36. How to avoid crosstalk in PCB design?
Answer: The changed signal (such as a step signal) propagates along the transmission line from A to B. A coupled signal will be generated on the transmission line CD. Once the changed signal ends, that is, when the signal returns to a stable DC level, the coupled signal will not exist. Therefore, crosstalk only occurs in the process of signal transition, and the faster the signal edge changes (conversion rate), the greater the crosstalk. The electromagnetic field coupled in space can be extracted as a set of countless coupling capacitors and coupling inductances, where the crosstalk signals generated by the coupling capacitors can be divided into forward crosstalk and reverse crosstalk Sc on the victim network. The two signals have the same polarity; coupling The crosstalk signal generated by the inductor is also divided into forward crosstalk and reverse crosstalk SL, which have opposite polarities.
The forward crosstalk and reverse crosstalk generated by the coupling inductor and capacitor exist at the same time and are almost equal in size. In this way, the forward crosstalk signals on the victim network cancel each other due to opposite polarities, and the reverse crosstalk polarity is the same, and the superposition is enhanced. The modes of crosstalk analysis usually include default mode, tri-state mode and worst-case mode analysis. The default mode is similar to the way we actually test crosstalk, that is, the infringing network driver is driven by the flip signal, and the victim network driver maintains the initial state (high level or low level), and then calculates the crosstalk value. This method is more effective for crosstalk analysis of unidirectional signals. The tri-state mode means that the infringing network driver is driven by a flip signal, and the tri-state terminal of the victim network is put into a high-impedance state to detect the size of crosstalk. This method is more effective for bidirectional or complex topology networks. The worst-case analysis refers to keeping the driver of the victim network in the initial state, and the simulator calculates the sum of the crosstalk of all the default victim networks to each victim network. This method generally only analyzes individual key networks, because there are too many combinations to be calculated, and the simulation speed is relatively slow.
37. In the EMC test, it was found that the harmonics of the clock signal exceeded the standard very seriously, but the decoupling capacitor was connected to the power pin. What aspects should be paid attention to in PCB design to suppress electromagnetic radiation?
Answer: The three elements of EMC are the radiation source, the transmission route and the victim. The propagation route is divided into space radiation propagation and cable conduction. So to suppress harmonics, first look at its propagation path. Power supply decoupling is to solve the conduction mode propagation, in addition, the necessary matching and shielding are also needed.
38. In PCB design, the ground wire is usually divided into protective ground and signal ground; the power ground is divided into digital ground and analog ground. Why should the ground wire be divided?
Answer: The purpose of dividing the ground is mainly due to EMC considerations, worrying that the noise of the digital part of the power supply and the ground will interfere with other signals, especially the analog signal through the conduction path. As for the division of signal and protection ground, it is because the consideration of ESD static discharge in EMC is similar to the role of lightning rod grounding in our lives. No matter how it is divided, there is only one final earth. It’s just that the noise is released in different ways.
39. In PCB design, is it necessary to add a ground shield on both sides when laying clocks?
Answer: Whether to add a shielded ground wire depends on the crosstalk/EMI situation on the board, and if the shielded ground wire is not handled well, it may make the situation worse.
40. Are the near-end crosstalk and far-end crosstalk related to the frequency of the signal and the rise time of the signal? Will it change as they change? If there is a relationship, can there be a formula to explain the relationship between them?
Answer: It should be said that the crosstalk caused by the infringing network to the victim network is related to the changing edge of the signal. The faster the change, the greater the crosstalk caused (V=L*di/dt). The influence of crosstalk on the judgment of digital signals on the victim network is related to the frequency of the signal. The faster the frequency, the greater the impact.
41. When designing the PCB board, there are the following two stacking schemes: Stacking 1 》Signal 》Ground 》Signal 》Power +1.5V 》Signal 》Power +2.5V 》Signal 》Power +1.25V 》Power +1.2V》 Signal》Power+3.3V 》Signal》Power+1.8V 》Signal》Ground》Signal Lamination 2 》Signal》Ground》Signal》Power+1.5V 》Signal》Ground》Signal》Power+1.25V 1.8V 》Power+2. 5V 1.2V 》Signal 》Ground 》Signal 》Power +3.3V 》Signal 》Ground 》Signal
Which lamination order is preferred? For Stack 2, do the two split power layers in the middle affect the adjacent signal layer? These two signal layers already have a ground plane to give the signal as a return path.
Answer: It should be said that the two types of cascades have their own advantages. The first type ensures the integrity of the plane layer, and the second type increases the number of ground layers, which effectively reduces the impedance of the power plane, which is good for suppressing system EMI. In theory, the power plane and the ground plane are equivalent to AC signals. But in fact, the ground plane has better AC impedance than the power plane, and the signal is preferably the ground plane as the return plane. However, due to the influence of the thickness of the stack, for example, the thickness of the medium between the signal and the power layer is less than the thickness between the ground and the ground, the split signal of the second mid-span also has the problem of incomplete signal reflow at the power supply separation.
42. When using protel 99se software to design the PCB, the processor is 8? C51, and there is a 40KHZ ultrasonic signal and 800hz audio signal in the crystal oscillator 12MHZ system. How to design the PCB to provide high anti-interference ability? For 89C51 As far as the single-chip computer is concerned, how big the signal can affect the normal operation of the 89C51? In addition to increasing the distance between the two, is there any other technique to improve the system’s ability to resist interference?
Answer: PCB design provides high anti-interference ability. Of course, it is necessary to reduce the signal change rate of the interference source signal as much as possible. The specific high-frequency signal depends on the level of the interference signal and the length of the PCB wiring. In addition to the separation distance, the problems of reflection and overshoot of interfering signals can be solved through matching or topology, which can also effectively reduce signal interference.
43. Do you need to pay attention to the distribution of power supply and wiring in PCB wiring as well as grounding? What kind of problems will it bring if you don’t pay attention? Will it increase interference?
Answer: If the power supply is treated as a plane layer, the method should be similar to the treatment of the ground layer. Of course, in order to reduce the common mode radiation of the power supply, it is recommended to shrink the power layer 20 times the height of the ground layer. If wiring, it is recommended to walk the tree structure, pay attention to avoid power loop problems. Closed-loop power supply will cause greater common-mode radiation.
44. I made a TFT LCD display. When others were doing EMC tests, the interference signal was transmitted through the space, which caused the image displayed on the screen to shake and the amplitude was quite large. Who can give advice and how to deal with it! Interference bursts are added to several signal lines. I don’t know the specific name. The interference signal is radiated through the signal line.
Answer: If it is a separate LCD, the burst test in the EMC test is almost unacceptable, especially when using the coupling clamp, it will be enough for you. If the LCD is used in the instrument, it is not difficult to solve, such as the decoupling process of the signal line, the conductive paste appropriately reduces the impedance of the LCD entrance, and the screen surface is added with a shielded conductive wire mesh.
45. Some time ago, EMC test showed that GSM fixed wireless phones have radiation spurious phenomena between 100MHz-300MHz. After that, the company sent me two shielded shell phones with electrostatic paint. The laboratory was not allowed to change the whole phone. I changed the shell of the electrostatic paint with ferromagnetic material to the phone to be modified and tested. The test results show that the previous spurious phenomenon is gone, but the main frequency has problems. The main frequency of the phone is 902MHz, but there are several frequencies between 905-910MHz. The basic situation is like this. During the modification, I only changed the case, and the circuit board and other hardware were not modified.
Answer: The types of phones can be understood as: wireless mobile phones, cordless phones, etc. Need to be clear: the type of phone, the operating frequency range of the host and the type of electrostatic spraying material of the chassis: such as ferromagnetic or non-ferromagnetic conductive materials and conductivity.
46. What are the side effects of choosing pour over all same net objects when using Protel Dxp solid copper? Will it cause interference signals to chaos on the whole board, thereby affecting performance? What I do is a low-frequency data acquisition card. This problem may not need to be worried, but I still want to find out.
Answer 1: For PCBs with mixed analog and digital, it is recommended to separate the analog, digital and ground, and finally ground at the same point, such as using “porcelain beads” or 0 ohm resistor connection. High-speed data lines should preferably have two ground wires running in parallel to reduce interference.
Answer 2: Pour over all same net objects have no effect on the performance of the signal, but only on the welding of some pads, and the heat dissipation is relatively fast. This should be good for EMI. Increase the contact area between the pad and copper.
Answer 3: Pour over all same net objects when solid copper is applied will not have side effects. It should be selected as the patterned pad instead of the solid pad, because the solid pad heat dissipates quickly, which may cause a tombstone situation during reflow soldering.
47. What are magnetic beads and what are their uses? What is the magnetic bead connection, inductive connection or 0 ohm resistance connection?
Answer: The magnetic beads are specially used to suppress high-frequency noise and spike interference on signal lines and power lines, and also have the ability to absorb electrostatic pulses.
Magnetic beads are used to absorb UHF signals. Like some RF circuits, PLLs, oscillating circuits, including UHF memory circuits (DDR SDRAM, RAMBUS, etc.), magnetic beads need to be added to the power input part, and the inductance is a kind of storage Energy components, used in LC oscillation circuits, low-frequency filter circuits, etc., its application frequency range rarely exceeds 50MHZ.
The function of the magnetic bead is mainly to eliminate the RF noise existing in the transmission line structure (circuit). RF energy is an AC sine wave component superimposed on the DC transmission level. The DC component is a useful signal that is needed, but the RF energy of RF is useless Of electromagnetic interference is transmitted and radiated (EMI) along the line. To eliminate these unwanted signal energies, chip beads are used as high-frequency resistors (attenuators). This device allows DC signals to pass through while filtering out AC signals. Usually the high frequency signal is above 30MHz, however, the low frequency signal will also be affected by the chip beads.
To correctly select the magnetic beads, you must pay attention to the following points:
1. What is the frequency range of unwanted signals;
2. Who is the noise source;
3. How much noise attenuation is required;
4. What are the environmental conditions (temperature, DC voltage, structural strength);
5. What is the circuit and load impedance;
6. Is there space for magnetic beads on the PCB board?
The first three can be judged by observing the impedance frequency curve provided by the manufacturer. Three curves are very important in the impedance curve, namely resistance, inductance and total impedance. The total impedance is described by ZR22πfL()2 := fL. Through this curve, select the bead model that has the largest impedance in the frequency range where the noise is desired to be attenuated and the signal attenuation is as small as possible at low frequencies and DC. In the case of chip beads, the impedance characteristics will be affected under excessive DC voltage. In addition, if the operating temperature rise is too high, or the external magnetic field is too large, the impedance of the beads will be adversely affected. Reasons for using chip beads and chip inductors: Whether to use chip beads or chip inductors mainly depends on the application. Chip inductors need to be used in resonant circuits. When it is necessary to eliminate unwanted EMI noise, the use of chip beads is the best choice.
48. I just did hardware design work. Ask you how to determine the capacitance value of the capacitor to eliminate crosstalk between the wires.
Answer: When wiring the PCB, you should be careful not to have too long parallel traces, especially high-speed or high-swing signals. If it cannot be avoided, keep a sufficient distance or add ground isolation. Parts subject to volume restrictions and high anti-interference requirements.
49. I found a headache when I actually made the product. When the developed prototype is placed on a car with a lot of interference, in order to solve the problem of freewheeling, a small battery is connected to the power supply of the car (a diode is added to prevent the voltage of the small battery from being pulled across.) But it was found that once connected to the car’s ground wire, the terminal will be interfered. Any good suggestions?
Answer: This is a very obvious EMC problem. The spark interference on the car will cause your terminal equipment to be interfered. This interference may be radiation or it may be conducted to your terminal.
There are many reasons for this problem:
1. The problem of grounding, the routing of the ground wire on the motherboard of your terminal, the situation of copper wiring
2. The shielding problem of the shell is a metal shell. Seal the non-metal shell with tin foil. You can try it.
3. The layout of the circuit board, the power part and the CPU part should be separated as much as possible, the power part wiring should be as thick as possible, as short as possible, the wiring rules are very important
4. The number of layers of the circuit board is more important. In general, the main board of electronic products on automobiles is preferably at least 4 layers. The anti-interference of the two layers may be poor.
5. Add a magnetic ring, you can consider putting a magnetic ring on the power line when doing the test
Of course, there may be many other solutions, the specific circumstances may be different, I hope it can help you
50. In the circuit, why is a resistor connected in series in SCL, SDA, and AS, and what effect does the size of the resistor have on the circuit?
Answer: The pull-up is to increase the ?q interference capability, generally the value is Vcc/1mA~10K; the series is used for damping, generally 33ohm~470ohm, that is, when the pulse frequency of the signal line is higher, it will be from one end of the line Reflected to the other end, which may affect the data and there is EMI, adding a resistor in the middle of the line will effectively control this reflection.
51. When doing CE/FCC test, if the radiation is too high at 200MHz and exceeds the acceptable range, how should it be eliminated, how should the magnetic beads be selected, and how should the radiation in the frequency-doubling part of the crystal be eliminated.
A: The question you are talking about is really too simple, there is no way to give you a very accurate answer, but based on my personal experience, give me some ways of thinking.
If you can be sure that it is frequency doubling, you should mainly deal with the device that generates the frequency doubling. This should be a goal. You can try it directly in the processing, and a simple shield will be made for the device that generates the frequency doubling (only need to The key to using a coke can as a shield is to pay attention to grounding.) In the test, see if the radiation value is reduced. If it is reduced, the source of the radiation is clear, and it is specifically shielded. If there is no change, you should focus on the exposed transmission line. If the transmission line can be grounded, it must be grounded. It is best to try it with a shielded cable to see if there is a change to confirm whether it is related to the transmission line. Finally, there is the shielding problem of the cabinet itself. This problem is more complicated and the cost is higher. The solution is only considered when there is no way. After trying these methods, the radiation value should be reduced.
52. I am writing a 2KW vacuum cleaner software recently. The function is realized, but I can’t pass EMC. Please give pointers, which algorithm is used on the software, you can pass EMC! The function is briefly described as follows:
1. Soft start and soft speed regulation function. (The so-called soft start is the slow acceleration of the motor, the speed will not change suddenly)
2. The speed of the motor can be adjusted.
3. The SCR is used to control the motor. The control method is chopping the sine wave.
In terms of hardware, the circuit is very simple, hardware processing EMC is only a 0.1uF safety capacitor.
Answer: It may take more time to communicate with the hardware, and it is difficult to solve with simple software.
53. The conversion frequency of DA in DECODER is radiated from the chip along the power supply and ground, which is 166M. I have connected a 1N, or 630P, or 30P on the power supply, but it never fails. Two-layer board, the power circuit is very short, please give some suggestions, and analyze the reasons that can not be filtered out.
Answer 1: The quality of the power supply is poor (load capacity), DA should use a separate power supply.
Answer 2: First check whether the output terminal is well grounded. Try stringing the signal output port to BEAD.
Answer 3: I think you can use its 100M magnetic bead loss number 166M high frequency.
54. To do multi-channel temperature acquisition, use K-type thermocouple, charge pump conversion module for power supply, signal conditioning part want to use AD620 and OP07 for second-level amplification, there are a few places that are not sure, please do Help!
One is the power supply. I now use a 12v battery for power supply and convert it to +/-12v with a charge pump. This voltage has a certain ripple, which is not conducive to signal collection. Should I use the battery voltage as a single power supply?
The second is whether the two signal terminals of the thermocouple can be directly input to the input terminal of the AD620 as in the example in the AD620 data sheet. I see that there is also an EMI FILTER part in the manual. How should this part be added to the measurement of the thermocouple? What? Should the cold end of the thermocouple be grounded or connected to a stable voltage?
Third, because the temperature I requested involves minus zero, the AD620 output will be subjected to in-phase amplification and inverting amplification before being sent to the A/D port. I plan to use OP07 to make a second-level filter. The first level is an infinite gain filter circuit. The second level It is a filter circuit with 2x in-phase amplification and 2x in-phase amplification. I wonder if this is possible?
Answer: If the cold end of your thermocouple is grounded (the end of many equipment thermocouples is grounded), and the temperature is measured below zero, you better use +/- power supply. This is the usual practice. The ripple of the power supply is better, but not necessarily positive and negative symmetry, you can add a stable LDO to achieve. Low-frequency filtering has a great influence on the results, but the first-level filtering should be able to meet, EMI part depends on your application environment. For multi-channel temperature measurement, you can put the multiplexer before the amplification to reduce the cost. The multiplexer should have a differential input, and the thermocouple input wire should also be a thermocouple type, which is quite expensive.
55. Some basic problems of electromagnetic compatibility: some EMC problems often encountered in certification.
A: The following are some of the problems that are summed up for electronic products.
The most common problems of general electronic products are: RE-radiation, CE-conduction, ESD-static electricity.
Communication electronic products include not only the above three items: RE, CE, ESD, and Surge–surge (lightning strike, thunder)
The most prone problems in medical devices are: ESD-static electricity, EFT-transient pulse anti-interference, CS-conducted anti-interference, RS-radiated anti-interference
For the dry areas in the north, the ESD-static requirements of the products are very high.
For areas like Sichuan and some southwest mines, EFT lightning protection requirements are very high.
56. How can I remove the electromagnetic interference in the IC?
Answer: The electromagnetic interference received by IC mainly comes from static electricity (ESD). To solve the IC from ESD interference, on the one hand, we must consider the ESD (and EMI) problem when laying the board, on the other hand, we must consider adding devices for ESD protection. There are currently two types of devices: varistor (Varistor) and transient voltage suppressor TVS (Transient Voltage Suppressor). The former is composed of zinc oxide, the response speed is relatively slow, the voltage suppression is relatively poor, and each time it is impacted by ESD, it will age until it fails. The TVS is made of semiconductor, with fast response speed, good voltage suppression, and can be used unlimitedly. From a cost perspective, the cost of varistor is lower than TVS.
57. Electromagnetic interference phenomenon performance: Especially GPS is used in PMP products, the function is MP4, MP3, FM FM + GPS navigation function, handheld vehicle dual-use GPS terminal products, handheld vehicle dual-use GPS navigation terminal must have A built-in GPS Antenna, so that the MCU, SDROM, crystal oscillator and other components on the GPS Antenna and GPS terminal products are prone to electromagnetic interference, which causes the GPS Antenna’s ability to receive stars to drop a lot, and there is almost no way to locate it normally. I don’t know if any GPS design developers have encountered such electromagnetic interference, and then take effective methods to solve such electromagnetic interference. What kind of solutions? ?
Answer 1: I think this problem is mainly caused by the circuit design. Most of the problems are caused by the poor protection and shielding of the circuit. My current customers have no confusion in this respect. They now have two parts of electromagnetic interference, but basically all of them are The electromagnetic interference of /bluetooth has been resolved, 2 The electromagnetic interference of the remote control, the solution: I have not found the answer to the first item, and the second item increases the effective distance of the remote control to 5M.
Answer 2: The distribution of each functional module on the PCB is very important. Before the PCB Layer, it is necessary to plan according to the current size, the crystal frequency of each part, and then the grounding of each part is very important. This is to solve the interference of common power and ground. According to the actual measurement, the spatial distance between the main oscillation sources has a great influence on the radiation, and a little distance will significantly reduce the interference. If the space is not allowed, it is necessary to shield it locally, but only if it is in the same ground area of the PCB, and then For the decoupling of the entrance and exit of the power supply, the magnetic bead capacitor is a good choice, and the inductance of the Bluetooth and GPS printable boards. It is also important to choose the conversion frequency of the power supply DC/DC. Do not let the frequency multiplication (multiple harmonics) coincide with the frequency of other circuits (especially acceptance). Some DC/DC frequencies are fixed, and a simple filter circuit can be used. . Co-frequency suppression is the main reason for the decline in the sensitivity of GPS reception and remote control reception. Also, the amplitude of the receiving circuit should be adjusted as small as possible, otherwise it will become a continuous source of interference. We inherited Bluetooth, GPS, another 2.4GHz transceiver, 433M remote control reception in a box, the effect is not bad, GPS reception sensitivity is very high.
58, encountered a single-chip system
1. MC908JL3 of the main control chip Motorola
2. 8M ceramic resonance
3. The power supply is connected by a cable
It is now that the conducted voltage in EMI exceeds a single point by 0.8dB at 24M. Please advise if there is any good way to suppress the over-standard. Include in adding magnetic ring, adding Y2 capacitor, etc. Is this frequency a conduction range or a radiation range?
Answer: In the end, is it the 24M standard in the EMI experiment or the 24M standard in the case of conduction? If the former is the radiation standard, then the latter is the standard.
59. Use the bidirectional thyristor to control the speed regulation of the DC motor, but the motor will interfere with the power supply and affect the zero-crossing detection, resulting in uncontrolled or speed change. Please advise!
Answer 1: The possibility of this phenomenon is as follows: 1. The motor belongs to a non-resistive load, so the phase shift occurs in the circuit, resulting in inaccurate control; capacitor filtering can be added; 2. The general bidirectional thyristor controls high power or large Current load, using zero-crossing conduction instead of phase modulation, can reduce the impact of EMC.
Answer 2: The flow-shift phase speed regulation is very common. If the hardware part of the zero-crossing detection is okay, the software processing method must be carefully improved. In one cycle (50Hz 20mS), the thyristor guide must be processed twice. Through, the delayed output time after detecting the zero crossing determines your phase shift angle,
60. Does the hero have done EMC design of V.35, E1, G.703 (6?K) and relay interface? Can you give some suggestions?
Mainly through the following standards:
GB/T 17626.12 (IEC61000-4-12) Electromagnetic compatibility test and measurement technology Oscillation wave immunity test
GB/T17626.2 (IEC61000-4-2) Electromagnetic Compatibility Test and Measurement Technology Electrostatic Discharge Immunity Test
GB/T 17626.3 (IEC61000-4-3) electromagnetic compatibility test and measurement technology RF electromagnetic field radiation immunity test
GB/T 17626.4 (IEC61000-4-4) Electromagnetic Compatibility Test and Measurement Technology Electrical fast transient pulse group immunity test
GB/T 17626.5 (IEC61000-4-5) electromagnetic compatibility test and measurement technology Surge impact immunity test GB/T 17626.6 (IEC61000-4-6) electromagnetic compatibility test and measurement technology RF field induced conducted disturbance immunity
A: These standards are some basic standards for EMC testing, and you need to determine specific indicators in conjunction with your products. Your interfaces are communication interfaces and generally have standard circuits. When the single board schematic filter design and the correct layout and wiring design of the PCB can generally pass the test, in other cases, EMC filtering and transient suppression devices need to be added, which needs to be combined with specific interface analysis.
61. The wiring cannot cross the gap between the divided power supplies. Which prawn can give a detailed explanation?
Answer: If a power layer is divided into several different power parts, such as 3.3V, 5V, etc., the signal lines should not appear on different power planes at the same time, that is, the wiring cannot cross the gap between the divided power sources Otherwise, there will be unnecessary EMC problems, the same is true for the ground, and the wiring cannot cross the gap between the divided grounds.
62. The current single-chip computer controls the pull-in of the AC contactor through a Darlington tube and a light-coupled control of a 12V relay. It often causes the reset of the single-chip computer at the moment of pull-in, and the reset pin is measured by the oscilloscope, and a valid reset signal can be detected (using three pins Reset IC). The single-chip microcomputer uses 5V power supply, 1000uF capacitors have been connected before and after the 5V voltage regulator tube, and no power fluctuation was found by oscilloscope detection. In addition, if the relay is unloaded (without AC contactor), no reset phenomenon is found. How do you solve it?
Answer 1: A resistance and capacitance absorption circuit can be connected in parallel with a resistor and a capacitor in series at both ends of the AC contactor coil. The capacity of the capacitor is between 0.01UF and 0.47UF. Now, the withstand voltage is preferably higher than the rated voltage of the coil. 3 times, does this work?
Answer 2: This should be caused by the EMC interference generated when the AC contactor operates. The resistance-capacitance absorption of a friend upstairs is a good solution. At the same time, you can also consider trying a high-voltage capacitor in parallel with 100P to 47P at the output contact of the 12V relay.
Answer 3: It is effective to add RC absorption to the AC contactor. But you also check your power circuit to see if your CPU power trace is too long, try to remove the capacitor on the power pin of the chip, and also the LC part can also add LC absorption circuit, as much as possible Absorb interference from the power supply.
Answer 4: First, check whether there is the same phenomenon without load, and judge the discharge problem by grade. It is not necessary to connect the optical lotus first, then the relay. If the reset still occurs if the optical coupling is not connected, check if the hardware output port is short-circuited with the reset. If there is no reset, the optical coupling can be connected but not the relay. It is also possible to reset the ground wire is too thin, the ground of the reset pin is too close to the photocoupler and away from the power supply, the current limiting resistance of the photocoupler is too small, resulting in an instantaneous increase in ground potential. When wiring, the CPU should be far away from the high current device, and the ground wire should be star-shaped single-point ground. If the reset still occurs, it is the electromagnetic interference caused by the change of the relay coil and the arc or the large load. It can be solved by shielding and eliminating contact arcing. In most cases, the power supply is not handled properly, the ground wire or +5V wire is too long or too thin,Unreasonable CPU location.
63. Can AC filter and DC filter be used interchangeably? Generally speaking, AC line filters can be used in DC applications, but DC line filters must not be used in AC applications. Why?
Answer: The bypass capacitor used in the DC filter is a DC capacitor, which may be damaged due to overheating under AC conditions. If the withstand voltage of the DC capacitor is low, it will be damaged due to breakdown. Even if these two situations do not occur, the common mode bypass capacitors in general DC filters have a large capacity, and excessive leakage currents may occur in AC applications, violating safety standards.
64. In a box-type device, such as an Ethernet switch or a PC, there is a chassis ground and a circuit ground. I found that some devices connect two grounds with capacitors, some with 0 resistance, and some with ferrite. Connect, which one is right?
Answer: We generally use 102 high voltage ceramic dielectric capacitors.
65. What does “institutional protection” mean? Is it the protection of the chassis?
Answer: Yes, the case should be as tight as possible, use less or no conductive materials, and be grounded as much as possible.
66. How does the product use metal as the shell (such as aluminum, stainless steel, etc.) to the ESD protection of the product? What should be done better?
Answer: All products are made of metal shells. If the grounding is not good, it is not conducive to ESD protection, but as long as the grounding is done, there will be no problems. As for how to ground, it depends on the specific situation of the equipment. If it is a large-scale equipment, you can directly connect the ground through the equipment. The effect will of course be very ideal.
67. Why can’t the spectrum analyzer observe transient interference such as electrostatic discharge?
Answer: Because the spectrum analyzer is a narrow-band swept receiver, it only receives energy in a certain frequency range at a time. Transient interference such as electrostatic discharge is a kind of pulse interference. Its spectrum range is very wide, but the time is very short. In this way, the spectrum analyzer observes only a small part of its total energy when the transient interference occurs, which cannot reflect the actual Interference situation.
68. When diagnosing electromagnetic interference problems in the field, it is often necessary to use a near-field probe and a spectrum analyzer. How to make a simple near-field probe with coaxial cable?
Answer: Strip the outer layer (shield layer) of the coaxial cable to expose the core wire, wrap the core wire into a small ring (1~3 turns) with a diameter of 1~2 cm, and weld it to the outer layer.
69. Measuring the biomagnetic information of the human body is a new medical diagnostic method. This biomagnetic measurement must be performed in a magnetic field shielding room. This shielding room must be able to shield the alternating electromagnetic field from the static magnetic field to 1 GHz. Please suggest this Shielded room
Design.
Answer: First of all, consider the choice of shielding materials. Since shielding the magnetic field with very low frequency, it is necessary to use materials with high magnetic permeability, such as permalloy. Since Permalloy is processed, the magnetic permeability will be reduced and heat treatment must be performed. Therefore, the shielding room should be assembled, and assembled from plates. Each plate is processed according to the design in advance, then heat treated, transported to the site, and installed very carefully. The joints of each sheet should overlap to form a continuous magnetic path. The shielding chamber constructed in this way can have better shielding effectiveness against low-frequency magnetic fields, but the gap will produce high-frequency leakage. In order to make up for this deficiency, the outer layer of the permalloy shielding room is welded with aluminum plates to form a second layer of shielding, which shields the high-frequency electromagnetic field.
70. When designing a shielded chassis, what factors should be used to select shielding materials?
Answer: From the perspective of electromagnetic shielding, the main type of shielded electric field wave should be considered. For electric field waves, plane waves or high frequency magnetic field waves, general metals can meet the requirements. For low frequency magnetic field waves, materials with higher magnetic permeability should be used.